For String Bio, methane isn’t just a greenhouse gas emitted by belching cows — it’s also a viable source of high-quality protein with a multitude of applications.
String Bio produces alternative proteins and biostimulants (substances used to improve crop resilience) through an innovative bacterial fermentation process. Their raw material is methane, a nefarious greenhouse gas that traps 80 times more heat than carbon dioxide.
Last year, the startup participated in The Liveability Challenge, an annual competition in search of sustainability solutions. As one of the competition’s finalists, String Bio was awarded a 1-year venture building package at The Circularity Studio.
In this interview with Eco-Business, Dr Subbian talks about the challenge of commercialising products during a pandemic, the rising reputation of fermented proteins, and the sustainability solutions that inspire her.
How has the Covid-19 pandemic affected your plans for String Bio?
The Covid-19 pandemic has delayed our plans to enter the protein market. Our products are market-ready, but product testing has really slowed down. On the positive side, Covid-19 has drawn attention to sustainability and food safety. This pandemic has shown that we need to take a pause to look at how we manufacture today, and it’s brought alternative markets that are cleaner, safer, and more sustainable to the forefront.
What do you see as the best use of your technology?
I think the real power of our methane conversion technology is in its multiple uses. The more we can use our core technology, the better. String Bio is launching products in two key sectors: alternative proteins for human and animal nutrition, and biostimulants for agriculture.
Each use has different benefits. For example, the aquaculture sector requires a high quality, protein-dense ingredient to feed fish sustainably. We also have products in our pipeline that can provide stress tolerance and immunity enhancement for poultry. With human nutrition, it’s about enabling very clean protein that can go into various products, like meatless burgers or protein shakes. As higher temperatures and harsher environments strain these sectors, we can provide support with an alternative protein supply, while reducing methane emissions on the supply-side.
What challenges have you faced in developing your project?
Methane is a tough substrate to work with. Over the last six years, we’ve built efficiency in the conversion process so that we can use it as a raw material. Developing our technology required us to work across many disciplines; our work has been the innovation we’ve done in chemistry, engineering and biology to overcome the challenges of working with methane.
Now, our challenge is building the business up. Fortunately, there’s been tremendous focus on the alternative protein market in the last few years. There are three big ‘buckets’ in alternative protein today. There’s cellular agriculture, using stem cells to grow meat; plant-based meat alternatives; and microbial, or fermented protein. We’ve seen some of the barriers surrounding fermented protein start to come down; it’s becoming more accepted by consumers as awareness grows. What seemed to be impossible a few years back is much easier now.
Where do you see yourself in five years?
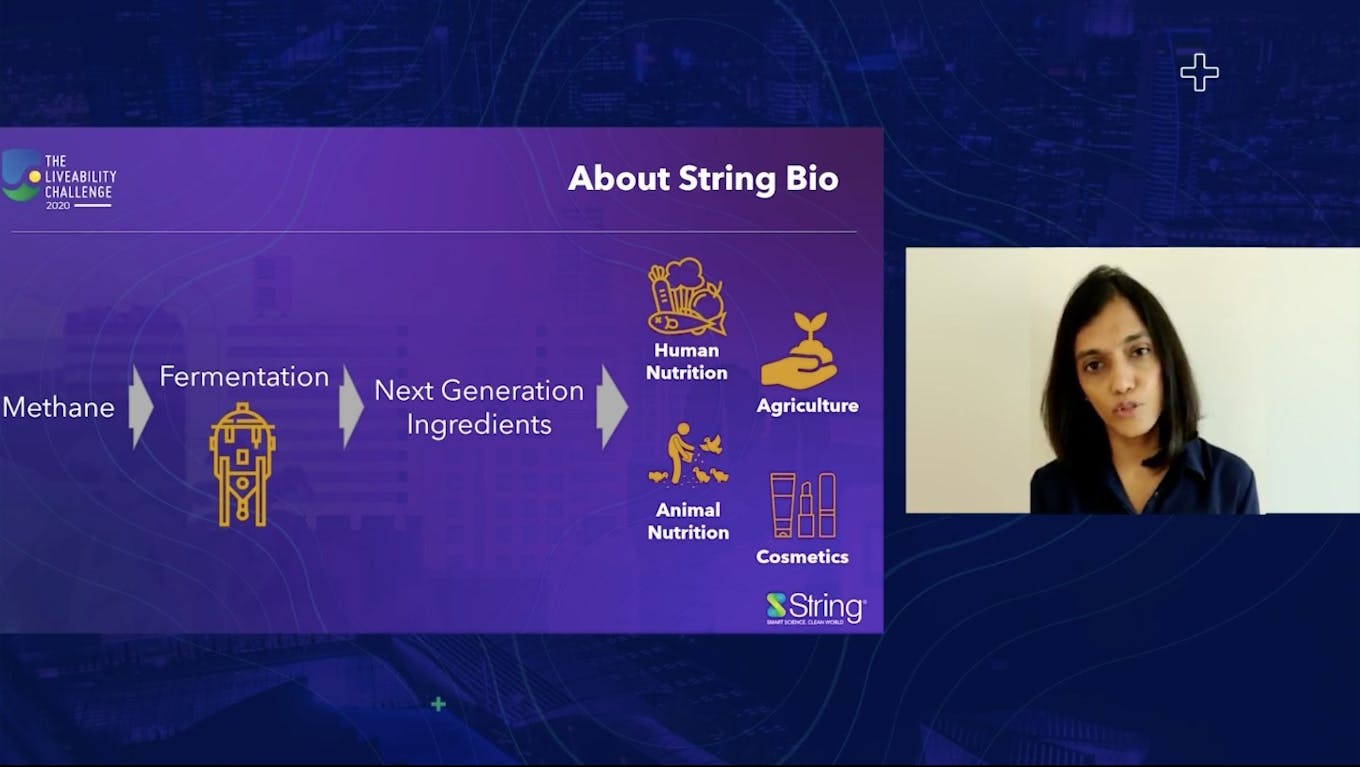
Ezhil Subbian presenting on behalf of String Bio at The Liveability Challenge 2020. Image: Eco-Business
Our goal in five years is to have facilities around the globe manufacturing alternative proteins, bio-stimulants, and other new products. We strongly believe that if the protein industry is going to grow and continue providing basic nutrional needs, then supply chains also need to grow efficiently. We want to enable localised manufacturing and consumption. The big advantage of methane is that it’s a raw material that’s present globally.
What other sustainability innovations are emerging right now that inspire you?
The discussion around biodegradable packaging has really picked up steam recently. Dealing with plastic and non-biodegradable waste is a huge issue for countries like Singapore, so I’m excited to see how packaging waste solutions will grow. We also have some interesting compounds that we can develop for biodegradable polymers.
Having lived in the United States for 14 years and grown up in India, one problem I’ve noticed is that solutions that work for developed countries are applied to developing countries. It’s good to see that a recent movement has emerged to develop more energy-efficient solutions for densely populated countries. Just look at the toilet challenge that Bill Gates has been pushing forward: in the West, the toilet system requires a lot of water to deal with waste. Instead of taking that system and fitting it to Asia, the challenge says, ‘given today’s technological knowledge, there must be a less energy-dense way to do this.’ Solutions can’t always be one-size-fits-all. We need to develop solutions based on the raw materials and ecosystems present in the region.
What advice do you have for the sustainability entrepreneurs of the future?
We also need to help the sustainability entrepreneurs of today, because solutions are needed now. It’s time to acknowledge climate change. Surface temperatures and greenhouse gas emissions are going up. We need solutions that also take the environmental toll of manufacturing into account. My advice for any sustainability entrepreneur: we need your solution now. Stay with it and make sure your solution sees the light of day.
This story is part of a series on the finalists of The Liveability Challenge, an annual search for solutions to make Southeast Asia’s cities cleaner, greener places to live and work, backed by Temasek Foundation. Applications to join The Liveability Challenge 2021 are open until 15 April 2021.